Prefab housing is on the rise, because of quite a lot of elements together with labor and materials shortages, and let’s face it, the necessity for extra reasonably priced housing. Mordor Intelligence suggests prefabricated housing will high at the very least $143.55 billion by the top of 2025 and it’ll soar to $198.25 billion by 2030, which is a 6.67% progress charge. I believe even the Queen of Prefab would approve these numbers!
The U.S. Census Bureau estimates there are roughly 7 million prefabricated properties in the US, which represents about 7.5% of all single-family properties. Additionally, greater than 80% of contractors have already embraced off-site constructing methods like modularization.
The development is basically selecting up pace, particularly since conventional homebuilding strategies require roughly seven months from groundbreaking to completion. That is difficult with labor shortages, climate delays, and rising materials prices.
Let’s have a look at one instance of prefab. In 2017, father-son duo Paolo and Galiano Tiramani started researching and testing supplies and strategies that will allow the automotive-style mass manufacturing of homes, and BOXABL was born.
BOXABL’s major innovation is its patented folding constructing system that permits environment friendly manufacturing unit manufacturing and achievable transportation logistics. With its strategies and know-how, it may produce an entire house each 4 hours. That is considerably quicker than the seven months for standard building.
Different benefits embody with the ability to get rid of weather-related delays since it’s inbuilt a manufacturing unit setting, and standardized parts allow economies of scale. Additionally, vertical integration of producing processes reduces supply-chain vulnerabilities and automatic manufacturing reduces labor dependency.
BOXABL designed and produced the primary few prototypes of the Casita and showcased it on the Intl. Builders’ Present in 2019. At 361-sq.ft., the Casita mannequin has full fixtures and utilities for roughly $60,000.
In Might 2021, BOXABL obtained a federal contract price greater than $9,000,000 to construct and ship 156 Casitas to be used at a army base. That very same 12 months, BOXABL broke floor on its first manufacturing unit in Las Vegas, Nev. The next 12 months, BOXABL partnered with homebuilder DR Horton, which included an order for 100 Casitas. In 2023, BOXABL constructed second and third manufacturing unit buildings.
Right this moment, BOXABL additionally has Child Field, which is a 120-sq-ft residing house constructed to the RV code. The corporate can be increasing the product line to permit clients to stack or join Packing containers to construct totally different constructing varieties together with single household dwellings, townhouses, and condo properties.
Seeking to the long run, BOXABL is at the moment within the planning phases for the subsequent step—a multimillion sq. foot manufacturing unit, which it’s calling the BOXZILLA Manufacturing facility. This manufacturing unit would home superior automation gear.
After all, this is just one instance. We’ve got seen different instances of homebuilders specializing in prefab building. For example, we now have written about Clayton’s CrossMod properties, which mixes off-site building with site-built options. We’ve got additionally coated Mighty Buildings, which is a 3D printing firm that’s opening a manufacturing unit to print climate-resilient properties for the U.S. market.
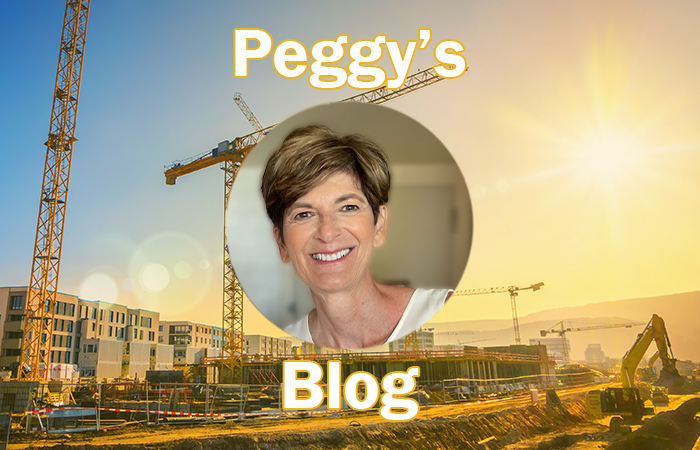
Prefab is a development that’s selecting up pace each in residential and industrial building, providing alternatives to construct extra reasonably priced housing with a smaller workforce. It should definitely be a development to proceed to observe within the days forward.
Need to tweet about this text? Use hashtags #building #IoT #sustainability #AI #5G #cloud #edge #futureofwork #infrastructure #prefab