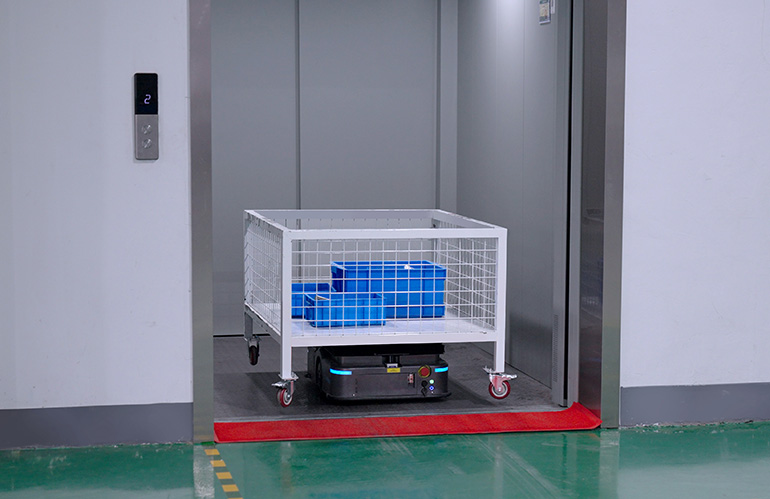
The RDS fleet administration system can serve in situations akin to multilevel motion. Supply: SEER Robotics
Underneath the wave of Trade 4.0, robotics know-how is more and more permeating manufacturing and logistics processes. Nevertheless, attaining environment friendly collaboration and optimum useful resource allocation in complicated multi-machine operations, cross-regional scheduling, and diversified situations stays a essential problem. SEER Robotics stated its M4 Sensible Logistics Administration System, powered by its core module—the RDS Fleet Administration System—gives an revolutionary resolution.
The Shanghai, China-based firm defined how its Useful resource Dispatch System (RDS) fleet supervisor can elevate effectivity throughout 4 various situations by means of clever scheduling.
RDS permits cross-floor, cross-region collaboration
In giant factories, duties spanning a number of flooring and areas have gotten commonplace, requiring robots to coordinate with elevators, automated doorways, and different good units. SEER Robotics stated its RDS system acts as a “central neural community” by integrating with enterprise-level enterprise software program akin to manufacturing execution methods (MES) to allow information change and activity distribution.
Case research: Zhejiang Tailin Bioengineering
Zhejiang Tailin Bioengineering’s RDS system interfaces with its MES, enabling automated activity allocation and robotic execution. As an example, throughout cross-floor transportation, the system dynamically synchronizes elevator schedules with robotic routes, making certain clean activity transitions.
The corporate also can provoke duties by way of MES and monitor logistics in actual time, attaining improve in cross-floor operational effectivity.
Dynamic world planning resolves congestion
In complicated environments with slender aisles or human-robot collaboration, path conflicts and congestion are frequent. The RDS system employs dynamic world planning to research real-time robotic positions, activity priorities, and environmental adjustments, optimizing multi-robot pathfinding and site visitors management to forestall deadlocks.
Case research: WINFAT Holdings
With 44 clever forklifts below RDS coordination, the system resolved path conflicts throughout peak operations at WINFAT Holdings Ltd. By dynamically adjusting routes and prioritizing duties, the corporate achieved 100% accuracy in human-robot collaboration and a 300% increase in total manufacturing effectivity.
Pre-Loading Mode eliminates empty runs
Empty robotic runs are a standard supply of useful resource waste in logistics. The RDS system introduces revolutionary “ride-sharing” and “pre-loading” modes. Utilizing world task-allocation algorithms, it assigns new duties to robots nearing completion and directs multi-warehouse robots to select up items from the closest areas, minimizing idle journey and enhancing warehouse effectivity.
Case research: Chinawrr Automated Pallet Warehouse
Utilizing real-time RDS information, Chinawrr’s warehouse dynamically adjusts inbound/outbound activity allocation, attaining a unilateral throughput of 290 pallets per hour and a 20% improve in storage effectivity, with empty runs decreased to under 5%.
Manufacturing beats simulation: Precision deployment of robots
In precision manufacturing, controlling manufacturing beats immediately impacts effectivity and high quality, stated SEER Robotics. The RDS system permits speedy simulation modeling, permitting firms to check robotic deployment by dynamically scaling robotic numbers and simulating concurrent duties.
Case research: Electrolux’s Swedish manufacturing facility
SEER Robotics’ RDS system optimized robot-system interfacing and resolved communication delays in semi-finished product transportation. This reduces manufacturing beat errors to a a lot decrease stage and will increase output capability for Electrolux.
RDS and the way forward for fleet administration
The RDS system’s worth lies in its “world optimization” logic and “dynamic adaptation” capabilities, in accordance with SEER Robotics. By driving selections by means of information, it could actually improve cross-regional collaboration, complicated path planning, and useful resource utilization.
As synthetic intelligence and Web of Issues (IoT) applied sciences converge, the fleet administration system will additional transcend situation limitations, changing into the core engine of commercial automation, the firm stated.
Register now so you do not miss out!